It is amazing to think how three little words can influence your buying choices when it comes to certain products. These three words not only convey where it originates from but also its build quality and furthermore, your confidence in said product – “Made in (Insert Country Here).” Did you know that Made in Germany, as far as recent studies go, is the most respected “Made in” moniker around, especially when you consider under a century ago “Made in Germany” was originally a British label designed to disparage German-made goods?
While I’m sure the Germans are aware of how well respected “Made in Germany” is, this hasn’t stopped them from taking it a step further; to a higher designation called “Miesterkries”, a term which translates in English to “Master Circle”. Being a part of this upper circle is a sign of excellence, where Miesterkries states that “A brands character and their virtues – from tradition and craftsmanship to design, precision and innovation – shape the culture and represent high-end Made in Germany, both nationally and abroad.” Of course, there are a few names most if not all of you know of, such as Leica and Porsche but also Glashütte Original – who I recently paid a visit to, at their manufacture in watchmaking town of Glashütte.
THE ARRIVAL – DRESDEN MUSIC FESTIVAL
We arrived in the afternoon, a day before the actual manufactory tour, in Prague? – strangely enough landing in Prague is actually more convenient. Upon arrival we were whisked away and headed for a short drive to our Dresden Hotel. A quick pitstop and we headed straight to the Glashütte Original boutique, to have a look at the 2019 novelties (one of which we posted a couple of weeks ago). On the eve of our factory visit, we attended the Dresden Music Festival, of which Glashütte Original is a sponsor, where legendary Violinist, Joshua Bell, accepted his Glashütte Original Music Festival Award. The evening was filled with music played by Camerata Salzburg featuring Joshua Bell.
THE GLASHÜTTE ORIGINAL FACTORY TOUR
The next day is where it would all begin, and we’d get to see the inner sanctum that is Glashütte Original. We were chauffeured from our Hotel to the luscious green rolling hills of Glashütte, Saxony – the watchmaking capitol of Germany. Once we arrived at the manufacture, we were ushered into the main building, which felt almost hospital-like; the dust free environment did have touches of character, where beneath the vast rising glass ceiling stood display cabinets that showed-off historical Glashütte Original timepieces.
After a bit of conversation with some fellow editors, who were on the same factory tour as us, we were guided through some doors in to the manufactory. Now, unfortunately for us on this tour, nobody was allowed to take photos but luckily for us, Glashütte Original provided us with a photographer that we could ask to take particular shots we required during the tour – leaving us free to fully immerse ourselves in the manufacture.
Glashütte Original pride themselves on consistent precision and so it is very natural that to achieve this level of accuracy, modern tools must be used; thus milling, drilling and engraving are done with the very latest generation of computer-controlled machining; nothing unusual we haven’t seen before. Once the pieces have been milled, they’re microscopically checked for any deviations, which can have an impact on the overall tolerance. The movement base plates, bridges and shafts are all made using brass, however, it’s in the next department where we start to see where human touch comes into play.
It is in the finishing department and assembly departments, where things start to get very, very interesting. Our next stop is where we would see technology meet art. This is where the base plates are adorned with perlage and even on the sections that will never see the light of day, until they are serviced that is, by hand. There were a great number of circular graining sized pegs used just for this purpose. Then there is the Glashütte signature three-quarter plate and bridges that are decorated with Glashütte ribbing. And there there’s the hand-engraved balance cock that supports the balance wheel staff.
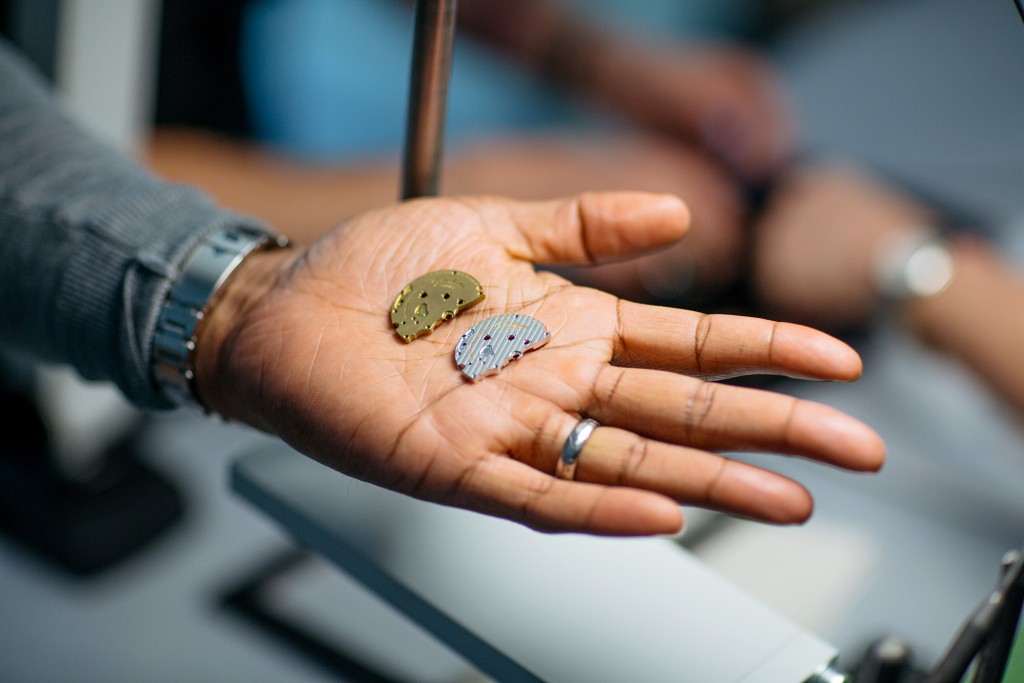
It was interesting to learn that all engraving, polishing, perlage and Glashütte ribbing was applied before movements were coated with a layer of rhodium. And it is before this process that all engraving is sealed with a solution, to preserve these engravings. Once the movement parts have been dipped in a coat of rhodium, all engravings that were preserved are then removed in a sonic cleaning solution. While this may seem like a rather mundane process, it is pretty time consuming, but the end result is stunning.
From here we moved into a newly created department that has been setup for waterproof testing, which wasn’t really supposed to be a part of the tour but Glashütte Original couldn’t help showing-off this new space. To enter into this new department, we were required to put on some dustproof white coats and go into a dust removal partition before entering. Once inside, we witnessed the waterproof test, steps that wasn’t anything out of the ordinary, but it was nice to see Glashütte Original’s commitment to this new process and to add, if I’m not wrong, the first of its kind for Glashütte Original.
Then we moved onto the department that is responsible for, arguably the most important aspect of a wristwatch: the assembly of the movement. Glashütte Original spend an enormous amount of time and effort into this horological process and we were given a chance at trying to assemble and disassemble some components of a couple of calibres, with some of us more fruitful than others. Walking around the assembly department it was interesting to see just how much attention is lavished on each component.
Just as we thought we’d come to the end of the tour; we were shuffled along to a finishing section that allowed us to get a feel of how to perform different finishing techniques. First, we tried a bit of polishing of a swan neck regulator, then tried our hand at some polishing of other components using some older techniques, which Glashütte Original still use on certain movements. This is something we have tried doing before and it’s still no easier the second time round. Getting the perfect polished surface is extremely difficult and this is something that Glashütte Original pride themselves on. Each watch calibre is lavishly worked on by hand can take several days before its finished to the Glashütte Original standards. For example: it can take up to 45-minutes just to polish a swan neck regulator and a further 1-hour to polish each bridge angle. Lastly, we were all given a chance to blue some screws used on selected calibres, which was a fun finishing touch to the tour.
FINAL WORD
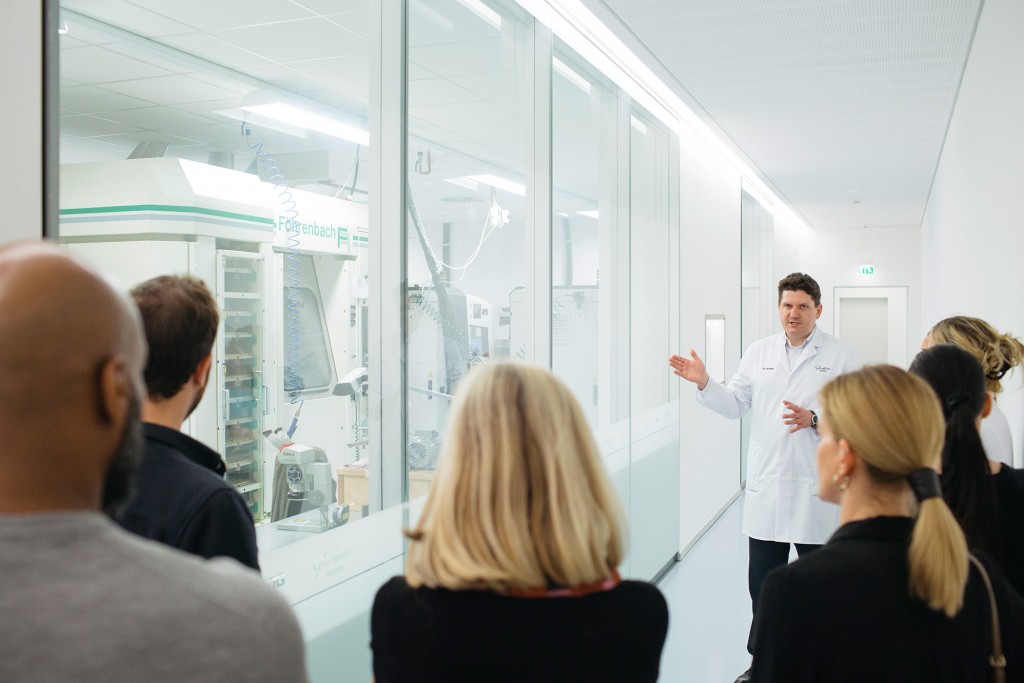
For me, this was a rather enjoyable experience and seeing the inner sanctum of where these pieces of art are created was pretty cool, and it has honestly given me greater appreciation of Glashütte Original’s timepieces. The attention to detail lavished on their timepieces was a massive eye-opener but more importantly I was able to understand and see the true value within their timepieces. Each timepiece is truly a work of art, crafted by the humble watchmakers of Glashütte Original. Even more pleasing is the fact that just next door is the German Watch Museum Glashütte dedicated to giving you a glimpse into the history of the brand, as well as other German watch manufacturers.
From the outside looking in, one would assume that the German watchmaking industry is rather young but touring the Glashütte Original manufacture, displays Germany’s deep rooted watchmaking history. So while “Swiss Made” may be the seal of quality you are used to seeing when glancing down at your watch, let us not forget that “Made in Germany” is a seal of excellence.